Scopo dei materiali di rivestimento
Rivestire la superficie esterna dei tubi in acciaio è fondamentale per prevenire la formazione di ruggine. La ruggine sulla superficie dei tubi in acciaio può comprometterne significativamente la funzionalità, la qualità e l'aspetto estetico. Pertanto, il processo di rivestimento ha un impatto considerevole sulla qualità complessiva dei tubi in acciaio.
-
Requisiti per i materiali di rivestimento
Secondo gli standard stabiliti dall'American Petroleum Institute, i tubi in acciaio dovrebbero resistere alla corrosione per almeno tre mesi. Tuttavia, la richiesta di periodi di protezione antiruggine più lunghi è aumentata, con molti utenti che richiedono una resistenza dai 3 ai 6 mesi in condizioni di stoccaggio all'aperto. Oltre ai requisiti di longevità, gli utenti si aspettano che i rivestimenti mantengano una superficie liscia e una distribuzione uniforme degli agenti anticorrosivi, senza sbavature o colature che potrebbero compromettere la qualità visiva.
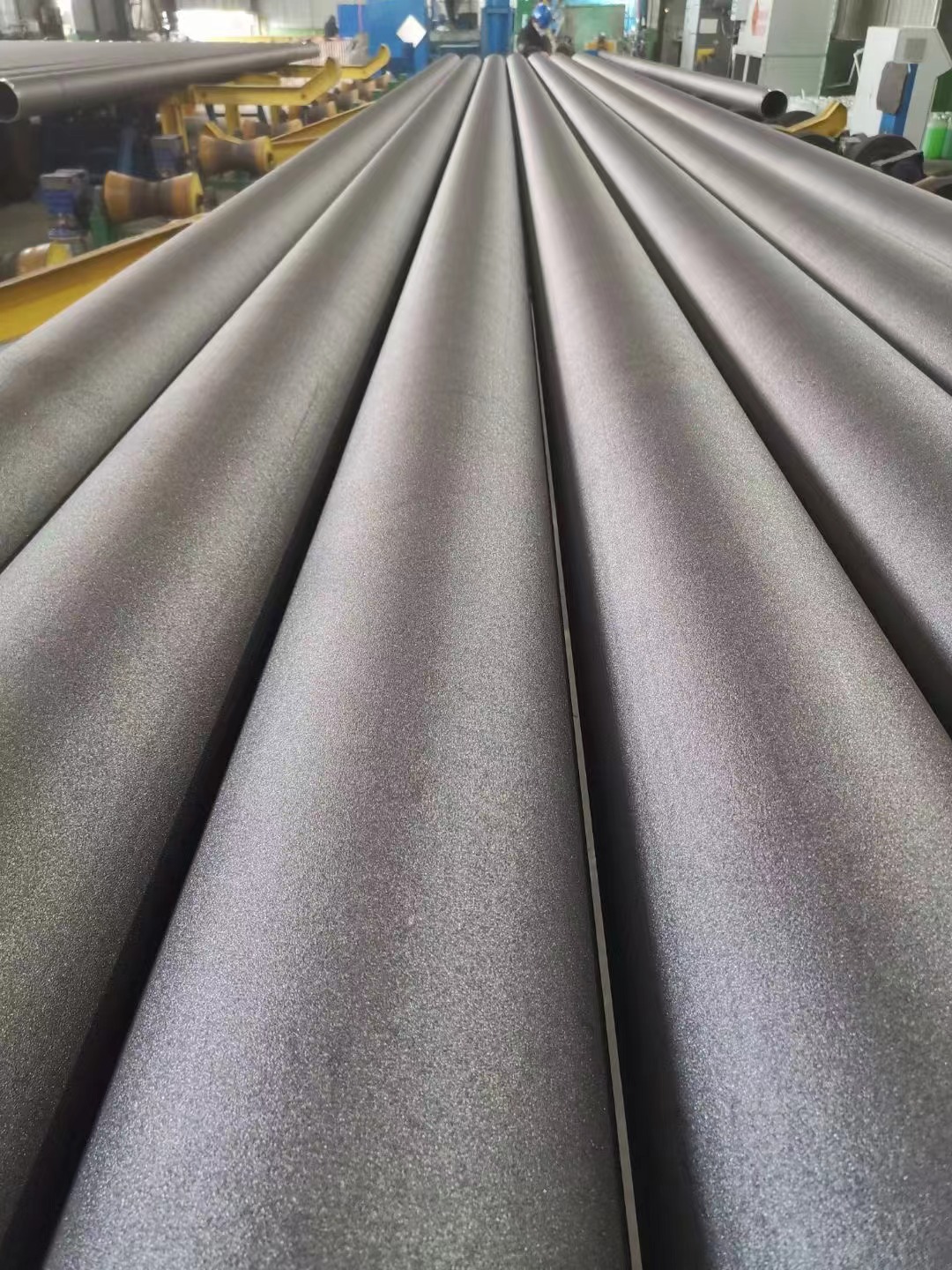
-
Tipi di materiali di rivestimento e relativi pro e contro
Nelle reti di tubazioni sotterranee urbane,tubi d'acciaioSono sempre più utilizzati per il trasporto di gas, petrolio, acqua e altro ancora. I rivestimenti per queste condotte si sono evoluti dai tradizionali materiali bituminosi a materiali in resina di polietilene e resina epossidica. L'uso dei rivestimenti in resina di polietilene è iniziato negli anni '80 e, con diverse applicazioni, i componenti e i processi di rivestimento hanno subito progressivi miglioramenti.
3.1 Rivestimento in asfalto petrolifero
Il rivestimento in asfalto di petrolio, uno strato anticorrosivo tradizionale, è costituito da strati di asfalto di petrolio rinforzati con tessuto in fibra di vetro e una pellicola protettiva esterna in cloruro di polivinile. Offre un'eccellente impermeabilità, una buona adesione a diverse superfici e un ottimo rapporto qualità-prezzo. Tuttavia, presenta alcuni svantaggi, tra cui la sensibilità alle variazioni di temperatura, la fragilità alle basse temperature e la tendenza all'invecchiamento e alla fessurazione, soprattutto in terreni rocciosi, che richiedono misure protettive aggiuntive e un aumento dei costi.
3.2 Rivestimento epossidico di catrame di carbone
La resina epossidica a base di catrame di carbone, realizzata a partire da resina epossidica e asfalto di catrame di carbone, presenta un'eccellente resistenza all'acqua e agli agenti chimici, alla corrosione, una buona adesione, resistenza meccanica e proprietà isolanti. Tuttavia, richiede un tempo di polimerizzazione più lungo dopo l'applicazione, rendendola suscettibile agli effetti avversi delle condizioni meteorologiche durante questo periodo. Inoltre, i vari componenti utilizzati in questo sistema di rivestimento richiedono uno stoccaggio specializzato, con un conseguente aumento dei costi.
3.3 Rivestimento in polvere epossidica
Il rivestimento a polvere epossidica, introdotto negli anni '60, prevede la spruzzatura elettrostatica di polvere sulle superfici di tubi pretrattati e preriscaldati, formando uno strato anticorrosivo denso. I suoi vantaggi includono un ampio intervallo di temperature (da -60 °C a 100 °C), un'elevata adesione, una buona resistenza al distacco catodico, agli urti, alla flessibilità e ai danni da saldatura. Tuttavia, il suo film più sottile lo rende suscettibile ai danni e richiede tecniche e attrezzature di produzione sofisticate, ponendo sfide nell'applicazione sul campo. Pur eccellendo sotto molti aspetti, è carente rispetto al polietilene in termini di resistenza al calore e protezione complessiva dalla corrosione.
3.4 Rivestimento anticorrosivo in polietilene
Il polietilene offre un'eccellente resistenza agli urti e un'elevata durezza, oltre a un ampio intervallo di temperature. Trova ampio utilizzo nelle regioni fredde come la Russia e l'Europa occidentale per le condotte, grazie alla sua superiore flessibilità e resistenza agli urti, soprattutto a basse temperature. Tuttavia, permangono delle difficoltà applicative su tubi di grande diametro, dove possono verificarsi cricche da stress e l'infiltrazione d'acqua può causare corrosione al di sotto del rivestimento, rendendo necessarie ulteriori ricerche e miglioramenti nei materiali e nelle tecniche applicative.
3.5 Rivestimento anticorrosivo pesante
I rivestimenti anticorrosivi ad alta resistenza offrono una resistenza alla corrosione significativamente superiore rispetto ai rivestimenti standard. Presentano un'efficacia a lungo termine anche in condizioni difficili, con una durata superiore a 10-15 anni in ambienti chimici, marini e con solventi, e superiore a 5 anni in ambienti acidi, alcalini o salini. Questi rivestimenti presentano in genere spessori del film secco compresi tra 200 μm e 2000 μm, garantendo protezione e durata superiori. Sono ampiamente utilizzati in strutture marine, apparecchiature chimiche, serbatoi di stoccaggio e condotte.
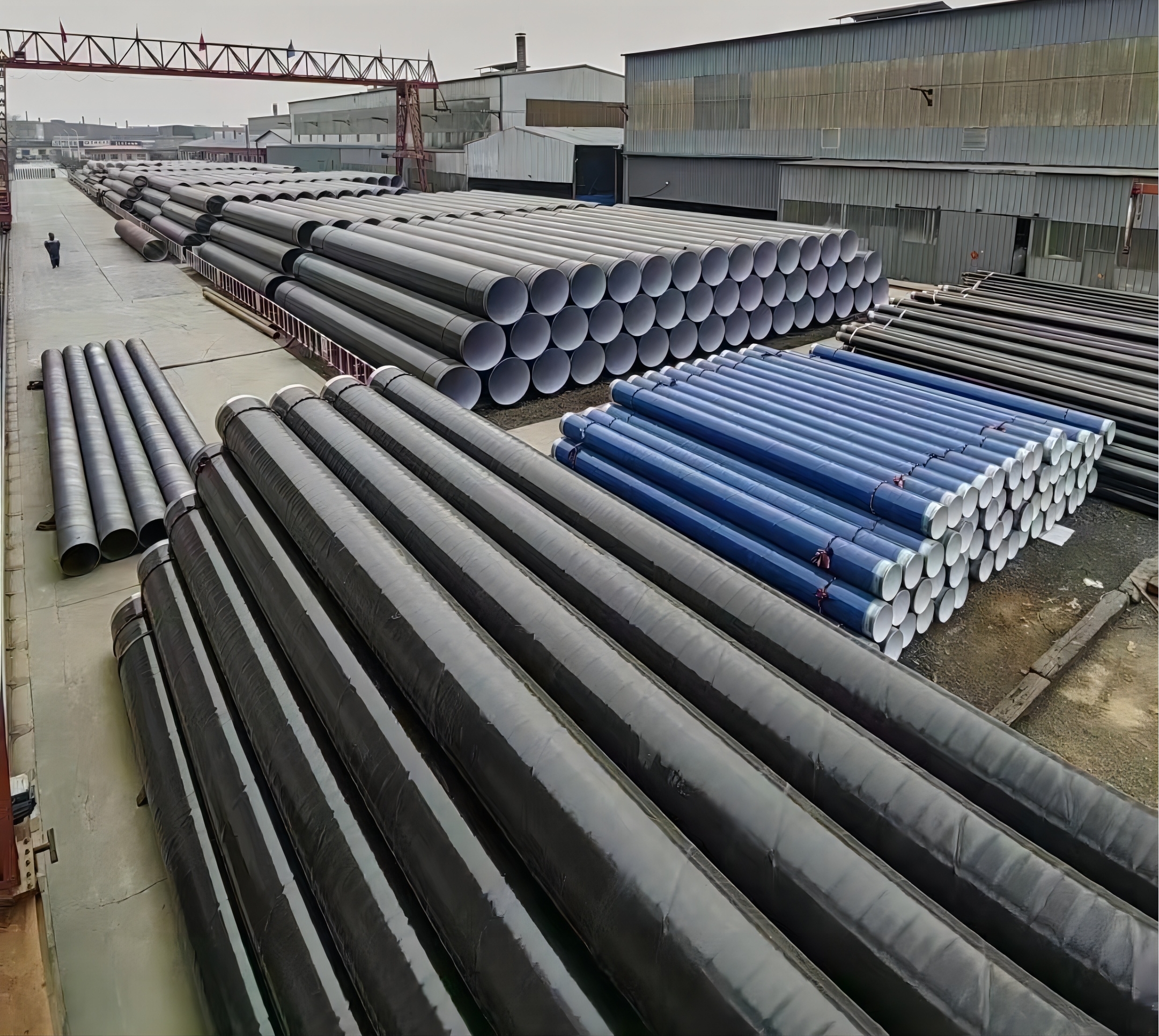
-
Problemi comuni con i materiali di rivestimento
Tra i problemi più comuni dei rivestimenti rientrano l'applicazione non uniforme, il gocciolamento degli agenti anticorrosivi e la formazione di bolle.
(1) Rivestimento non uniforme: la distribuzione non uniforme degli agenti anticorrosivi sulla superficie del tubo determina aree con spessore di rivestimento eccessivo, con conseguenti sprechi, mentre le aree sottili o non rivestite riducono la capacità anticorrosiva del tubo.
(2) Gocciolamento di agenti anticorrosivi: questo fenomeno, in cui gli agenti anticorrosivi si solidificano sotto forma di goccioline sulla superficie del tubo, influisce sull'estetica senza influenzare direttamente la resistenza alla corrosione.
(3) Formazione di bolle: l'aria intrappolata nell'agente anticorrosivo durante l'applicazione crea bolle sulla superficie del tubo, influenzando sia l'aspetto che l'efficacia del rivestimento.
-
Analisi dei problemi di qualità del rivestimento
Ogni problema nasce da una varietà di ragioni ed è causato da una varietà di fattori; e un fascio di tubi in acciaio evidenziato dalla qualità del problema può anche essere una combinazione di diversi fattori. Le cause di un rivestimento non uniforme possono essere approssimativamente suddivise in due tipi: il primo è il fenomeno di disuniformità causato dalla spruzzatura dopo che il tubo in acciaio è entrato nella camera di rivestimento; il secondo è il fenomeno di disuniformità causato dalla mancata spruzzatura.
La causa del primo fenomeno è ovviamente facile da individuare: l'attrezzatura di rivestimento, quando il tubo d'acciaio viene spruzzato a 360° con un totale di 6 pistole (la linea di rivestimento ne ha 12), è dotata di un sistema di spruzzatura. Se ogni pistola spruzza con una portata diversa, si verificherà una distribuzione non uniforme dell'agente anticorrosivo sulle diverse superfici del tubo d'acciaio.
Il secondo motivo è che, oltre al fattore di spruzzatura, esistono altre cause per il fenomeno del rivestimento irregolare. Esistono molti fattori, come la ruggine in entrata nel tubo d'acciaio e la rugosità, che rendono difficile la distribuzione uniforme del rivestimento; la superficie del tubo d'acciaio presenta una pressione dell'acqua residua quando l'emulsione viene applicata sul rivestimento, a causa del contatto con l'emulsione stessa. In questo modo, il conservante ha difficoltà ad aderire alla superficie del tubo d'acciaio, impedendo il rivestimento di alcune parti del tubo d'acciaio, con conseguente disuniformità del rivestimento dell'intero tubo d'acciaio.
(1) La causa delle gocce di agente anticorrosivo. La sezione trasversale del tubo in acciaio è rotonda, quindi ogni volta che l'agente anticorrosivo viene spruzzato sulla superficie del tubo, l'agente anticorrosivo nella parte superiore e lungo il bordo scorrerà verso la parte inferiore a causa della gravità, dando origine al fenomeno delle gocce sospese. Un aspetto positivo è che nella linea di produzione del rivestimento della fabbrica di tubi in acciaio sono presenti forni che possono riscaldare e solidificare nel tempo l'agente anticorrosivo spruzzato sulla superficie del tubo in acciaio, riducendone la fluidità. Tuttavia, se la viscosità dell'agente anticorrosivo non è elevata; se il riscaldamento non è tempestivo dopo la spruzzatura; se la temperatura di riscaldamento non è elevata; se l'ugello non è in buone condizioni, ecc., si verificherà la formazione di gocce sospese.
(2) Cause della formazione di schiuma anticorrosiva. A causa dell'umidità ambientale del sito operativo, la dispersione della vernice è eccessiva e il calo della temperatura del processo di dispersione causerà il fenomeno della formazione di bolle nel conservante. L'umidità ambientale e le basse temperature causano la dispersione dei conservanti in minuscole goccioline, causando un calo della temperatura. L'acqua presente nell'aria con umidità più elevata, dopo il calo della temperatura, si condensa formando piccole goccioline d'acqua mescolate al conservante, che penetrano all'interno del rivestimento, causando il fenomeno della formazione di bolle.
Data di pubblicazione: 15-12-2023